Manufacturing
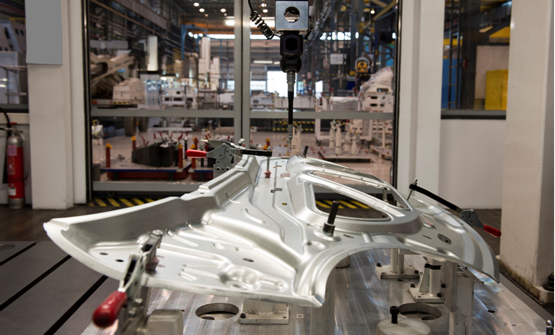
National Laser Restoration is dedicated to enhancing
manufacturing processes by providing innovative laser cleaning solutions. We offer both service and equipment solutions for businesses requiring laser cleaning or assistance establishing in-house operations. With our expertise in laser surface cleaning, advanced equipment, and a commitment to best practices, we help manufacturers streamline cleaning tasks, whether by
offering expert on-site cleaning services for components and equipment or by guiding companies through the setup and
integration of laser cleaning systems within their facilities. Our solutions focus on precision, safety, and environmental
sustainability, ensuring efficient, cost-effective results that
improve productivity and extend equipment lifespan.
When considering laser cleaning equipment in manufacturing, both for service providers and businesses looking to implement it in-house, several factors are essential for effective operation, safety, and cost-efficiency:
Surface Material and Contaminant Types
- Compatibility: Laser cleaning works well on metals and some other durable surfaces, but it might not be suitable for softer or more heat-sensitive materials. Contaminant Types: The laser can effectively remove rust, oxides, oil, grease, paint, and other residues without damaging the underlying surface. Testing may be needed to determine optimal settings.
Power and Laser Type
- Laser Power: Higher-powered lasers (e.g., 100W to 500W or more) are suited for industrial applications where quick cleaning of heavy contaminants is required. Lower power may be ideal for delicate surfaces.
- Laser Type: Pulsed lasers are typically better for applications requiring precise, non-destructive cleaning, whereas continuous-wave lasers may offer faster cleaning but with a risk of higher thermal impact.
Safety and Environmental Considerations
- Protective Measures: Laser cleaning produces fumes, potentially toxic particulates, and bright light, requiring ventilation, dust collection systems, and personal protective equipment (PPE) like laser goggles.
- Work Area Design: Enclosures and interlocks for laser operation help mitigate risks, especially for higher-powered systems in areas where personnel are present.
Process Control and Repeatability
- Automation Potential: For consistency, integrating laser cleaning with robotics or automation can improve throughput and reduce manual intervention, critical for in-house operations.
- System Programming: Ability to program laser settings for repeatability can make the cleaning process faster and more reliable, especially in high-volume or precision-driven environments.
Energy and Maintenance Costs
- Operational Efficiency: Lasers generally require lower energy compared to abrasive or chemical cleaning but may still need a substantial power supply, especially for high-output models.
- Maintenance: Routine calibration and maintenance of the laser system are essential to ensure long-term reliability and consistent cleaning results, especially in high-use scenarios.
Environmental and Regulatory Compliance
- Eco-Friendly:Laser cleaning is often more environmentally friendly than chemical methods, as it doesn’t require solvents. However, it still produces particulate waste that must be filtered and managed.
- OSHA and Other Standards: Compliance with occupational safety regulations, including laser safety (ANSI Z136 standards), is crucial to avoid fines or workplace hazards.
Cost and Return on Investment (ROI)
- Initial Investment: Laser cleaning equipment can have a high upfront cost but might reduce costs over time by eliminating the need for consumables like chemicals or abrasive media.
- Service Fees: For businesses offering laser cleaning as a service, pricing needs to reflect equipment costs, labor, and maintenance, while remaining competitive with other cleaning methods.
Scalability and Adaptability
- Modularity: Some laser systems offer modular setups that can be adapted or expanded based on the evolving needs of a facility.
- Surface Versatility: Businesses with diverse cleaning needs, such as those dealing with different materials and contaminant levels, benefit from a system that can easily switch between settings for different applications.
Training and Skill Requirements
- Operator Training: Laser cleaning requires specialized knowledge, particularly for higher-powered lasers. In-house technicians should be trained to adjust settings based on material type and contamination level.
-
Service and Support: Choose a laser manufacturer with strong customer support and training resources, as this can impact uptime and ease of troubleshooting.
laser cleaning’s flexibility and eco-friendly profile make it appealing in manufacturing. Careful consideration of material compatibility, safety, cost, and operational requirements will ensure it’s an effective, efficient solution, whether as an in-house process or a service offering.