HVAC
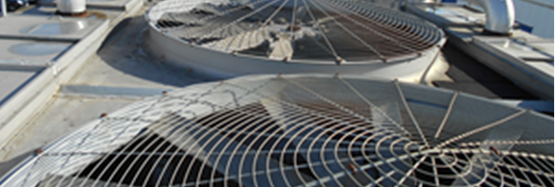
With over 60 years of experience in mechanical HVAC
refurbishment across building and process environments,
National Laser Restoration is a trusted partner for HVAC
companies and clients seeking to clean and maintain their
clients HVAC assets. Our extensive expertise enables us to
deliver tailored laser cleaning solutions that enhance the
performance and longevity of HVAC systems while ensuring
optimal efficiency and safety.
What to Consider
Cleaning HVAC equipment with lasers is an innovative approach that offers precise and effective removal of contaminants like
corrosion, dirt, and biofilm without damaging sensitive components. However, several considerations should be taken into account to ensure successful cleaning while maintaining equipment integrity.
1. Material Composition
- Understanding Materials: HVAC components are often made from various materials, including metals (like aluminum, stainless steel, and galvanized steel), plastics, and composites. Each material responds differently to laser cleaning, so it’s essential to choose the appropriate laser type and settings.
- Corrosion Levels: Assess the level of corrosion on cooling towers and other components. Different degrees of corrosion may require varying laser parameters to effectively clean without causing additional damage.
2. Type of Contaminants
- Identifying Contaminants: Common contaminants in HVAC systems include dust, dirt, grease, mold, and corrosion products. Understanding the specific contaminants will guide the selection of the appropriate laser settings and technique.
- Biological Growth: If there is biofilm or mold present, specific laser settings may be necessary to ensure effective removal while preventing potential damage to the underlying surfaces.
3. Laser Selection
- Choosing the Right Laser: Different lasers (e.g., fiber lasers, CO2 lasers) have unique properties suited for various materials and contaminants. Selecting the appropriate laser type is crucial for achieving optimal cleaning results.
- Wavelength Considerations: The wavelength of the laser affects its interaction with different materials. It’s essential to choose a wavelength that effectively targets the contaminants without adversely affecting the substrate.
4. Energy Settings
- Adjusting Power Levels: Proper calibration of energy density, pulse duration, and focus is crucial. Too high energy can lead to overheating and damage, while too low energy may not effectively clean the surface.
- Distance and Angle: Maintaining the correct distance and angle from the surface is important to achieve the best results. This can affect the effectiveness of the laser cleaning process.
5. Equipment Accessibility
- Accessing Components: Ensure that all parts of the HVAC system are accessible for laser cleaning, including hard-to-reach areas in ductwork and cooling towers. Consider using extension arms or specialized equipment for difficult access.
- Disassembly Requirements: In some cases, it may be necessary to partially disassemble components to achieve effective cleaning. This should be evaluated on a case-by-case basis.
6. Safety Precautions
- Personal Protective Equipment (PPE): Operators should wear appropriate PPE, including laser safety goggles, gloves, and protective clothing, to mitigate risks associated with laser operation and potential debris generation.
- Site Safety Measures: Ensure that the work area is secured and that bystanders are kept at a safe distance during the cleaning process.
7. Environmental Considerations
- Minimal Waste Generation: Laser cleaning produces minimal waste compared to traditional cleaning methods. However, dust and debris generated during the process should be contained and collected appropriately.
- Chemical-Free Cleaning: Laser cleaning eliminates the need for harsh chemicals, making it a safer choice for both the environment and personnel working in the HVAC system.
- Downstream Environmental Control: Lasers minimize the risk of downstream odors common with chemical cleaning process.
8. Testing and Trial Runs
- Conducting Tests: Before cleaning entire systems, perform tests on small areas to assess the effectiveness of the laser settings and the material’s response.
- Monitoring Results: Use the outcomes of test patches to refine the approach and optimize the cleaning process.
9. Protection of Sensitive Components
- Non-Damaging to Sensitive Parts: One of the significant advantages of laser cleaning is its ability to remove contaminants without damaging sensitive components such as bearings, fan wheels, drain pans, and other integral parts of HVAC systems. The precision of laser technology allows for targeted cleaning that protects these components from abrasion and wear, ensuring their continued functionality and longevity.
10. Post-Cleaning Assessment
- Inspecting for Damage: After cleaning, inspect the components for any signs of damage or stress that may have occurred during the cleaning process.
- Follow-Up Maintenance: Establish a maintenance plan to monitor the cleaned components and address any issues that may arise.
11. Professional Expertise
- Training and Experience: Proper training in laser operation and knowledge of HVAC systems is essential for achieving optimal results. Operators should be familiar with both the cleaning equipment and the HVAC components being serviced.
-
Collaboration with HVAC Specialists: Working alongside HVAC professionals can enhance the effectiveness of the cleaning process and ensure that best practices are followed.
Laser cleaning of HVAC equipment offers a powerful solution for removing contaminants while preserving equipment integrity, particularly for sensitive components. By considering the material composition, contaminant types, laser selection, safety measures, and professional expertise, technicians can successfully clean HVAC systems and improve their efficiency and longevity.